In the fast-paced world of steel supply, on-time deliveries are not just important—they’re crucial. To stay competitive, selecting a steel service center that excels in delivery efficiency, communication, and risk management is essential. This guide will help procurement professionals identify key qualities in a steel service company to ensure prompt and reliable deliveries.
Understanding Common Causes of Delivery Delays
To effectively evaluate steel service centers, let’s start by understanding what causes delays:
- Inventory Management: Poor management can lead to stockouts or overstock, impacting delivery times.
- Lead Times: Sudden spikes in demand can extend lead times, particularly when critical job completion dates exist.
- Quality Issues: Steel that doesn’t meet quality standards requires reprocessing or replacement, causing delays.
- Freight Challenges: Transportation issues, such as truck breakdowns or scheduling conflicts, can affect delivery schedules.
Strategies for Minimizing Wait Times
When choosing a service center, assess their strategies for maintaining on-time deliveries:
- Choose Reliable Centers: Select partners with a proven track record of on-time deliveries and high-quality service.
- Ensure Proper Equipment and Capacity: Confirm that the center has the right equipment and sufficient capacity to handle orders promptly.
- Maintain Accurate Inventory Management: Look for centers that keep precise inventory to fulfill orders efficiently.
- Streamline Processes: Efficient process flows, documented specs and streamlined procedures can expedite order processing.
Nailing Demand Forecasting
Examine how service centers manage demand forecasting. Top centers monitor market trends and price fluctuations to optimize inventory and secure steel at the right times. Proactive strategies, like setting contracts with release schedules months in advance, ensure timely availability of steel without unnecessary delays.
Managing Freight Challenges
Evaluate how centers handle freight challenges. The best centers build strong relationships with reliable transportation companies, ensuring their fleets are well-maintained and capable of timely, condition-appropriate deliveries.
Processed steel getting securely fastened to a Conestoga flatbed for safe transport.
Best Practices for Handling and Transporting Steel
Confirm that the service center adheres to best practices for steel handling and transport:
- Secure Steel Properly: Ensure steel coils are securely fastened during transport.
- Prevent Moisture Issues: Verify that steel is covered to avoid quality problems caused by moisture.
- Schedule Drivers Effectively: Ensure drivers have adequate hours and comply with transportation regulations to avoid delays.
Leveraging Technology for Enhanced Deliveries
Look for service centers that utilize advanced ERP systems integrated with shipping functions. These technologies streamline operations, automate processes, and reduce manual errors, contributing to faster and more reliable deliveries.
Communication is Key
Clear, honest communication is essential for managing wait times and ensuring on-time deliveries. Choose centers that are upfront about lead times and provide regular updates. Centers that actively seek and incorporate customer feedback are better equipped to enhance their services and maintain high-quality standards.
Balancing Speed with Quality
To ensure timely deliveries without compromising quality, evaluate how centers manage expedited orders. Effective centers have written procedures for expediting deliveries, ensuring that all steps are followed diligently. This approach helps balance the urgency of rush orders with maintaining high-quality standards.
Managing Risks in Expedited Deliveries
Expedited deliveries come with risks such as missed steps or errors. Select service centers that address these risks by documenting their procedures, maintaining transparent communication about potential delays, and quickly responding to disruptions like weather events or supply chain issues. Look for a service center that is ISO 9001 certified.
Conclusion
In the competitive steel service industry, choosing a service center based on their communication practices, ability to balance speed and quality, and risk management strategies will help you minimize delays and ensure timely deliveries of your steel orders. Partnering with centers that excel in these areas will enhance your buying experience and keep you ahead in the markets you serve.
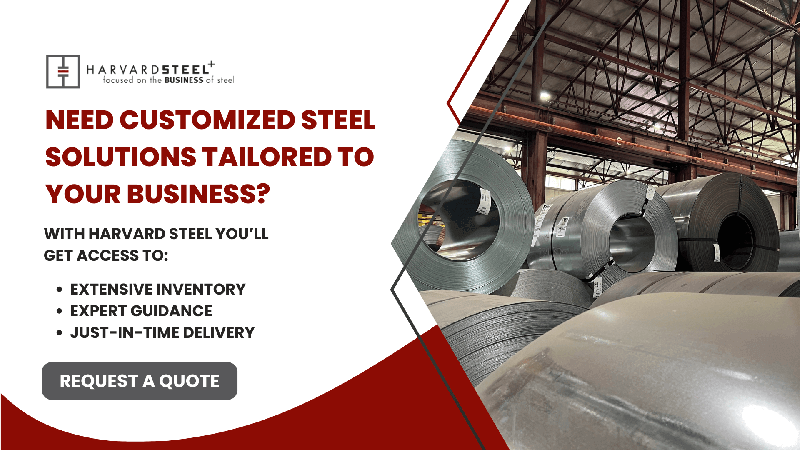
.png?width=290&name=image001%20(5).png)
COMMENTS